来源:心声社区
2019年2月24日,西班牙巴塞罗那,华为消费者BG总裁余承东刚从Mate X发布会的舞台走下来,没来得及反应,就被全球媒体记者们团团围住。大家饶有兴致地簇拥向前,都希望抢到第一时间上手体验的机会。超薄机身、独特外折、全面屏、独特转轴、革命性的交互等创新设计,获得业界广泛好评和关注。10月23日,华为宣布Mate X将于11月15日正式限量开售。这款被外界频频关注的折叠屏手机,是怎么做出来的?背后有哪些不得不说的故事?本文将从设计篇、结构篇、扇热篇三个部分为大家讲述。【设计篇】
折叠屏手机,要给你“好看”
Mate X ID团队
手机发展到今日,正面几乎只剩下一块屏幕,各个厂家都在极力隐藏不必要的干扰元素,整体形态都像鹅卵石一样平顺过度,各个部件之间严丝合缝。所以,作为设计团队,我们每个人心里都很清楚,如果折叠屏手机的颜值、体验不能匹配、甚至超过当前直板机,很难吸引消费者的兴趣。
从2015年开始,华为工业设计团队就开始向折叠屏手机ID设计探索,通过三大步骤,最终赋予Mate X令人惊艳的颜值。
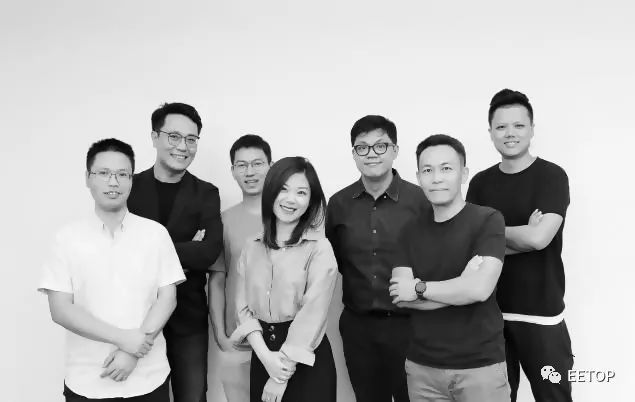
第一步:“骨架”采用外折叠方式
为什么要折叠?早在2015年,CBG & 2012硬工联合创新团队就开始了折叠机的探讨以及关键技术探索。当时只是觉得这可能是未来的一个手机方向,但很多人还是充满了怀疑:“直板手机已经够用了,既轻便又简单,想用大屏有pad就好了,而且pad市场逐年在萎缩,折叠没意义!”但是到了2017年,全面屏直板手机市场开始逐渐爆发,市场欢迎度很高。而且,移动高清视频、高分辨率摄影流量逐步提升,更大的屏幕显然可以获得更好的观看体验。大家意识到用户对屏幕尺寸的追求是逐步提升的。如果说全面屏是直板手机在有限尺寸范围内提升屏幕尺寸的最佳解决方案,折叠屏也许是未来更好的大屏解决方案。收纳状态下具有主流直板手机舒适的握持尺寸,展开使用时又能很好的享受大屏的体验。需求有了,实现的条件也在逐步酝酿。随着OLED(有机发光二极管)屏幕技术的发展,曲面屏幕迅速普及。尽管它们还不是真正意义上的可折叠屏幕,只能做到一次性固定形状的折弯,但到了2017年,很多厂家相继展示并表示已突破可折叠柔性屏技术,这也坚定了我们做折叠屏手机的信心。 外折还是内折?2015年,联合预研团队开始设想柔性折叠屏的应用形式:内折、外折、卷曲等。从2016年开始,各个面板厂家相继给出了可量产的屏幕技术规格,我们的探索最终聚焦到两种方式:内折(折叠后屏幕在内侧)、外折(折叠后屏幕在外侧)。两种方式各有好处。外折屏在观感上很酷,收纳状态下可以是双屏手机,有很多有趣的体验可以挖掘。比如给别人拍照时,后摄侧的屏幕可以作为镜像显示,被拍者可以随时看到自己在取景框中的状态,再也不用担心遇到不会拍照的男友了,自拍也可以使用更强性能的后摄来完成。打开的过程也很有趣,从一块小屏变化到大屏,是可以给人很大的震撼的。
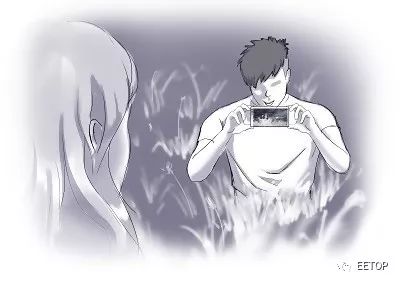
图1:双屏拍照体验示意图
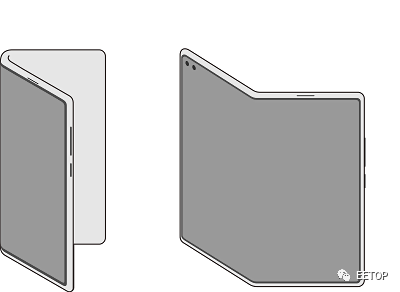
图2:外折屏示意图
内折更像书本的体验,非常有情怀感和安全感。但为了解决便捷使用的需求,业内通常会在外部多加一块屏。这样一来,在现有的柔性屏技术条件下,整机尺寸有所增加。
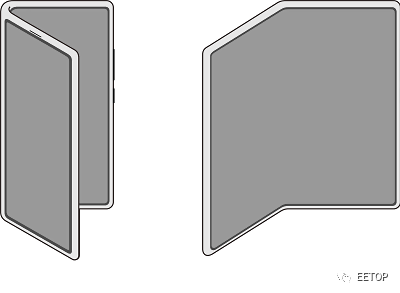
图3:内折屏+外屏效果图

图4:外折屏(Mate X)与内折屏(友商产品)的整机厚度(mm)对比基于这些考虑,我们最终选择外折作为首款折叠屏手机的“骨架”。但相比内折手机,外折也面临了更大的挑战:比如,柔性屏幕全部在外侧,日常使用的摩擦、撞击在所难免,防护成了最大的难题。在这个问题上,转轴设计团队和屏幕保护材料团队做出了关键的技术突破,尤其是转轴要做到“刚柔并济”。“柔”是指保证屏幕可自由弯曲不受拉扯或挤压;“刚”体现在任何弯折状态下,有足够的刚性支撑屏幕保持平整。同时,屏幕的触控层是由金属材质组成的,如果用屏幕包裹住整个机身,这对射频信号的影响是灾难性的。为此,结构和射频工程团队也做了足够多的探索,来攻克这个难题。 第二步:打造苗条“身材”和姣好“面容” Mate X在有限的空间中容纳了更多的硬件功能,囊括了更丰富的体验,但却依旧保持着简约外观。无论展开或者闭合状态均体现了全面屏的思考,无刘海,表面平整如一。但这样一个苗条“身材”和姣好“面容”,是费尽心思才得以设计出来的。摄像头是手机里最厚的器件,特别是随着手机拍照要求的不断提升,手机的摄像头的尺寸规格逐年递增,更好的画质必定意味着更大的模组尺寸。因此,摄像头的摆放位置及方式直接影响到了整机的轻薄和外观简洁性。而折叠机有上下两层,设计之初我们就坚持,整体厚度不能超出现有手机太多,否则市场接受度会很差。这样就意味着在展开状态下,摄像头必定会突出主机身很多。为了避免摄像头凸起,我们做了很多的讨论和取舍。有同事率先提出:机身前后都保留摄像头,怎么样?这个想法刚产生就被拍死了——这样一来,屏幕就要缩小,无法达成全面屏体验;如果将摄像头放在某一层的背部,那么另一侧就要有相应凹坑,展开使用时会很不美观;如果将摄像头放在正面屏幕侧凸起,一方面用户会跟现有手机的前摄对比,接受度很差,也会给全面屏的设计造成不小的影响。
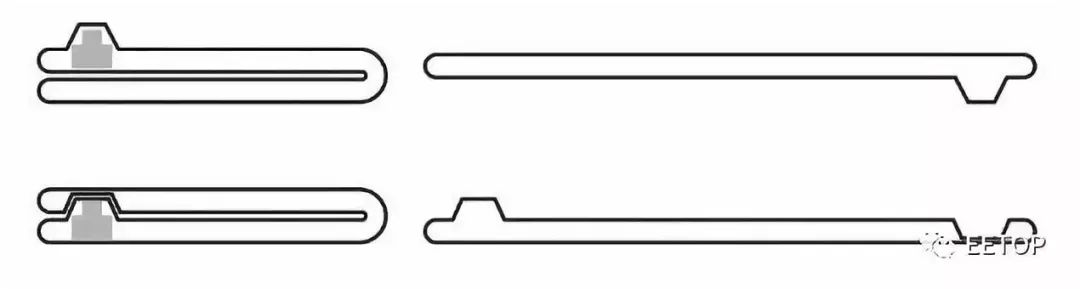
图5:摄像头的设计是一大难点这个问题困扰了我们很久。我们发动了很多设计师一起想如何解决这个问题。大家提出了多种方案,有升降摄像头、翻转摄像头、屏下摄像头等,前前后后做了十几个外观方案手板,始终找不到最佳方案。山穷水尽疑无路,柳暗花明又一村。就在我们冥思苦想之时,有一个同事跳出来问:为什么不能利用折叠机的双层空间来容纳摄像头?两层机身为什么一定要在侧面分割?一言惊醒梦中人。Mate X 的“非对称”架构由此而产生。如果把折叠机看成一个完整的O型形态的话,我们把两层的分界线移到了背部,于是形成了一个类似把手的结构,摄像头和所有的高规格器件都可以放在这儿。这种形态分割方式是最简洁的。

图6:Mate X非对称架构 这是一个一举多得的设计。首先,在收纳状态下,看不到任何额外凸起,展开时又可以作为握持的把手,不会因为机身面积变大而感到难以握持又或边缘硌手,带来良好的握持体验。其次,由于背部的屏幕可以配合后摄像头一起使用,所以正面的主屏也变成了干净的全面屏,还省去了一组前摄像头。同时,天线、USB等元器件也可以放置在把手位置,实现了高度一体化的设计,呈现更简约的外观效果。通过高度一体化、“非对称”的架构设计,我们赋予了折叠屏手机苗条、匀称的“身材”和姣好“面容”。 第三步:让折叠屏手机“表里如一”
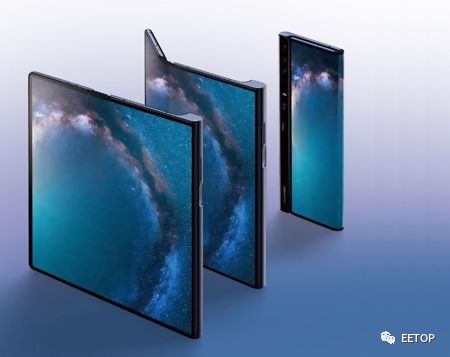
说实话,可折叠的柔性屏幕所有厂商都可以用,折叠屏手机的形态也可以被快速模仿,但能将这些融入自身核心设计中,并用好的厂商却不多。作为精密的传动部件,转轴位于折叠屏中间位置,是折叠屏手机最为核心的部分,具有中枢般的地位,这也是折叠屏手机研发过程中最难的地方。技术的难题姑且可以留给结构工程团队来实现。但作为工业设计团队,我们首要解决的是“颜值”的难题。如果转轴的外观设计不够简约美观的话,折叠屏手机闭合或展开时候,会有大的缝隙。在超薄的有限空间下,如何给予转轴这种复杂的运动结构简约和美观的外观设计?最初我们有很多备选方案,但外观都比较复杂。有的像坦克履带、有的像门窗的合叶,怎么看都太功能化,像是工业设备,很难匹配当下消费电子产品的简洁化趋势。为了保证外观简洁化的目标可以落地,我们深入到工程团队中学习基本的机构原理,一起参与详细设计。非常佩服我们工程开发团队的技术实力和耐心,对我们提出的很多苛刻的要求都尽力达成,最终用最简单的直线和弧形,在一开一合之间,完成了背部和侧边的遮蔽。最终的设计简化到只有两块金属滑板的状态,展开状态下只有一条接缝。整机外观看起来非常简洁、平整,同时也保证了结构的可靠性,实现了真正的“表里如一”。
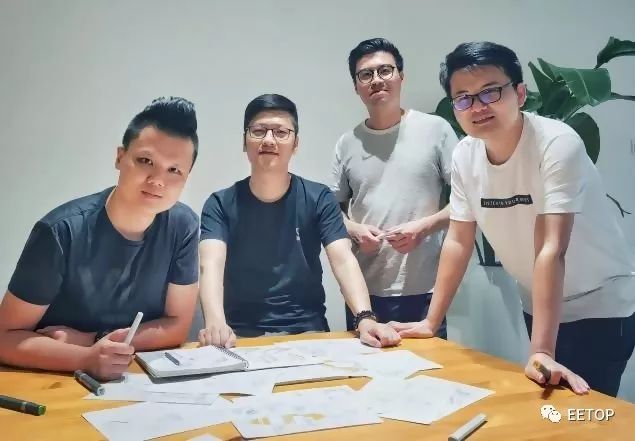
创新的高度一体化、非对称的外折叠架构、独特简约的转轴设计,让华为折叠屏手机拥有薄、轻、全面屏、无刘海、平整简洁令人惊艳的颜值,双面屏幕更将给用户带来无限潜力的丰富体验。作为折叠屏手机的工业设计团队,我们最得意的就是,用简约而不简单的设计,定义了折叠屏手机的设计方向,最感动的就是,整个项目团队,不论是设计人员、研发,还是供应链、制造人员,所有人都拧成一股绳,朝着一个方向努力,并为之付出百分之百的热忱,只为给消费者带来更好、更惊艳的体验。【结构篇】
转轴设计的“攀登”之路
Mate X转轴团队2019年2月,看着华为Mate X发布会的现场直播,听到余总介绍转轴开发的难点,表面平静的我们,内心早已澎湃不已。想起这三年,转轴设计团队从一个idea到最后的量产交付,整个开发历程就是不断解决难题的过程。
解决这些难题,就像攀登一座座山峰。每翻过一座大山,却发现有更高更陡峭的山峰在前面,直到登上最高峰,我们才明白,要做到业界第一,没有捷径可以借鉴,只有认准方向,坚持不懈把产品做到极致才能成功。
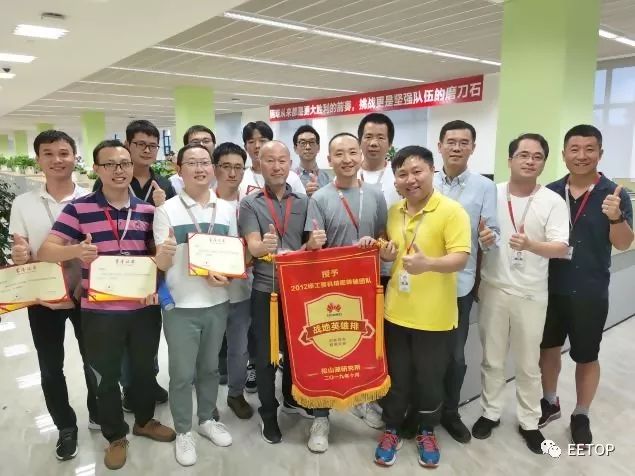
一、踏上“攀登”之路 2015年9月,随着业界Amoled(有源矩阵有机发光二极体或主动矩阵有机发光二极体)屏技术日趋成熟,我们认识到了折叠屏手机将会给消费者带来全新的用户体验,开发已经刻不容缓。为了充分挖掘折叠屏手机的价值,CBG & 2012硬工联合创新团队在上海进行了为期3天的封闭讨论。
我们从产品的折叠形态、显示区域的尺寸与长宽比、屏模组如何固定、屏与转轴的配合关系、转轴的功能、弯折角度和力度各个方面反复推敲。仅仅长宽比例一个问题,就做了十几种方案来实际体验。最终确认了内折/外折同时开发,重点研究双折形态,以功能样机为平台,攻克折叠手机的各个技术难关。
项目有两大技术关键点,屏和转轴。作为联合团队结构领域责任人,我们义不容辞接下转轴的开发任务。转轴设计团队定下的目标是将转轴的功能、可靠性与体验做到业界最佳。
“不就是个转轴嘛,小意思”。就这样,团队一共4人,带着无知者无畏的心态,开启了折叠屏手机转轴设计的攀登之路。
二、第一座山:想到的方案,专利都被“抢”了
被专利保护压得喘不过气
回到总部,我们立即召集结构专家商量对策。第一天讨论就发现了问题:这个转轴不能像普通转轴一样只转动,还要保证屏不褶皱。简单来说,转轴运动方式要像纸片一样摊开和折叠。如下图所示:
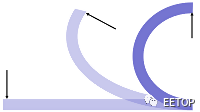
图1:转轴运动方式示意图
这种运动方式大家从来没有做过,没有经验可循。好在大家都是做结构出身,在学校都学过《机械原理》。我们把教材又拿出来边学边画,凸轮、连杆、齿轮、链条各种组合运用。大家相互打趣仿佛又回到了大学生活,开始了第二春。
经过几轮头脑风暴,大家想出了好几种实现方案,办公室里面洋溢着轻松愉快的氛围。
“不知道业界用的是什么方案呢?”项目经理一句话提醒了我们。对啊,折叠屏手机已经不是一个新概念了,早在2012年,友商已经开始专利布局,2016年已经有友商开发出样机并展出过。
我们开始调研业界折叠屏手机转轴的实现技术。随着调研越来越深入,心情也越来越沉重。因为我们想到的方案,基本上都有人抢先申请了专利。相关的专利数量超过50件,甚至连气囊充放气这种天马行空的想法,都申请了专利保护。设计人员最大的苦闷,莫过于发现自己的设计方案已经被别人申请了专利保护,这一件件专利就像一座大山压着大家喘不过气来。
但有山就有路。虽然有这么多的专利,为什么一直没有真正的产品出来?肯定有没想到的地方,有专利解决不了的问题。
随着研究不断深入,我们终于找到了突破点:转轴除了实现开合功能,还应该保证整个开合过程与屏的运动轨迹保持一致,让屏幕不论是折叠还是展平,都能得到最大的自由,转轴要成为屏幕折弯区坚强的后盾。这正是折叠系统稳定工作的关键,也是过往专利难以从方案变成现实的一大原因。
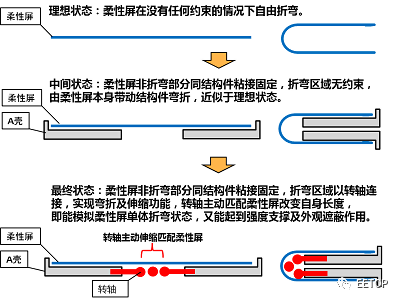
图2:工作原理概念图
自研“鹰翼式转轴”脱颖而出到了2017年初,团队确定了转轴详细规格以及整机堆叠方案。为了确保方案在业界的领先地位,我们在加大自身设计投入的同时,也在国内外的领先厂商与高校中寻求合作资源。
随着研发团队的壮大,我们兵分两路:一路是内部自研,国内与日本研究所专家联合设计攻关;另一路是外部合作,通过与高校及企业的机构设计专家们合作攻关。
转轴技术方案的开发是一个复杂的系统性的工程,为了让开发有序进行,我们经过严谨的反复讨论,将转轴分解为十来个子系统,如轨迹拟合、开合、阻尼、止位、润滑等,并结合团队成员的技能特点合理安排开发任务和计划。
随着研究的日益深入,我们也越来越了解到业界的水有多深。不同的传动对设计有哪些不同的侧重点与要求?什么材料既能耐磨又能承重?润滑油的粘稠度有什么影响?高低温环境又有什么影响?每一个细节都能作为一个专业课题深入研究下去。所幸有华为的大平台做依托,许多研究有专业的团队多年的成果积累,尤其是日本研究所的专家,凭借着在精密机构上多年摸爬滚打的经验,从设计到加工给了大家很大的启发。在和专家的交流与碰撞中,团队专业水平也得到了很大提升。
2017年底,历时三年,转轴设计团队的努力终于取得了成效。自研团队的“链式驱动”方案和外部合作的“摆杆驱动”方案被选为设计阶段的优选方案。
经过十几个日夜的赶工与组装,两种转轴的样品终于出炉。我们将装好的两种方案的整机放在同样的弯折机台上测试。结果显示,合作方案样品,一开测问题便突现出来。由于采用了多级的连杆方案,尺寸公差层层累计,到整机段装好屏后,用手挤压整机屏会拱起失效。而自研的链式驱动方案样品无论在哪个角度都能实现对屏的良好支撑。
2018年初,经过多方角逐,反复推敲,由转轴自研团队打造的“链式驱动”方案最终凭借其运动轨迹精准、功能全面、体积小,寿命稳定的优点一举胜出,确定作为量产方案落地正式产品项目。
该转轴设计方案是业界首创,不仅打破了业界的技术壁垒,而且通过发明专利建立了自己的技术控制点。后来大家给它起了一个很酷的名字“鹰翼式转轴”。
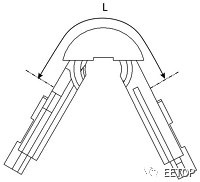
图3:鹰翼式转轴示意图
三、第二座山:史上最严苛的“瘦身”计划
经过一年多的开发与验证,项目由预研直接切换到量产交付,我们的团队也由原来的4人增加到了10多人。随着整机规格越来越清晰,重量和厚度成为转轴转量产的最大障碍。
折叠屏手机在折叠状态,相当于两个手机叠在一起。为了用户手持和随身携带方便,产品线确定折叠屏手机整机的尺寸规格,比当前业界最薄的手机还要薄0.5毫米。在此整机设计规格基础上,产品线对转轴提出了严苛的“瘦身”设计规格要求:长宽高尺寸要降低xx%以上,重量降低xx%以上,同时还要保证抗跌抗弯、弯折寿命等可靠性指标不下降。这个近乎苛刻的设计规格要求,成了挡在我们面前的第二座大山。
为了项目成功,除了胜利,没有别的选择!先从转轴自身简化做起。从头到尾一共一百多个零件,我们一个一个审视,从组件到次组件,再到零件:这两个能不能合并成一个?这里壁厚能不能挖掉一部分?螺钉能用更小的吗?为了0.01毫米的厚度大家都能争得面红耳赤。
“瘦身”不仅仅是压缩空间,减小零件尺寸那么简单。每一次“瘦身”都可能带来零件强度的降低,对产品的耐弯折寿命、抗反折能力等可靠性都会带来负面影响。因此,每精简一轮都需要仿真同事确认可靠性是否变差,哪里可以减薄,哪里不能动,甚至还要增厚,还需要在精密加工中心制作快速原型,组装整机测试验证。只有实际测试验证通过的减薄方案才能最终落地产品。经过一个多月的反复优化与验证,重量终于基本达成了规格要求。
可是为了“瘦身”,转轴的形状变得更不规则了,对外接口和电池、主板、天线等多个领域有冲突。我们又找到了各个领域的专家一起审视。仅仅为了满足两边共用同规格电池的要求,就尝试了三种不同的接口方式,不停地快速迭代优化。最终通过转轴两边不对称设计满足了各领域的要求。
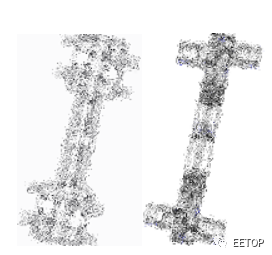
图4:瘦身前后对比图
四、第三座山:精密加工之难,让供应商都想放弃
极致的设计必然伴随极致的加工制造工艺。
整个转轴一百多个零件,材料涉及到金属粉末注射成型不锈钢、液态金属、注射成型硅胶等多种非常用材料工艺。组装段涵盖了业界转轴常用的基本所有组装工艺,如焊接、铆接、润滑、磨合等。从零部件的加工到组件的组装和测试都提出了全新的需求。
供应链技术资源很有限,供应商无法满足华为的加工制造工艺要求。在翻盖功能机时代,转轴行业曾十分兴盛。但在手机步入直板智能机时代后,转轴厂家也越来越难以为继。即使个别厂家也在探索新形态的突破,但由于没有大品牌厂家驱动,行业的整体投入以及创新力都比较弱。而且,做惯了PC机大尺寸产品转轴的组装厂也没有很好的经验可以借用。当我们将设计规格提供给供应商的时候,反馈的结果基本都是规格太严。
可整机的规格对转轴的诉求是没有讨价还价的余地。在没有退路的前提下,所有的成员深入到供应商的制造全流程中去,一个一个的工艺节点搜集问题,分析原因,讨论对策并跟踪落实到位。
由于折叠机需要不断的开合,对转轴的关键部件提出了超高强度及刚度的力学性能要求。尤其是转轴门板材料,有两个特别要求,一是外观要求高,二是适应重度摩擦场景。这是传统铝合金、不锈钢等手机结构材料远远不能满足的。
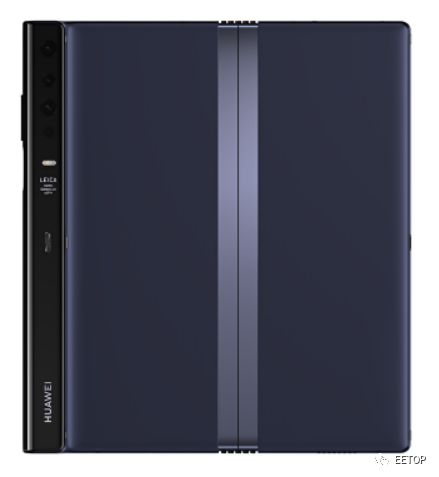
经过反复评估,我们决定选择具有高强度、高平面度属性的非晶合金作为转轴门板的材料。非晶合金自20世纪80年代诞生以来,以其超高强度高弹性的特殊性质,一直属于研究及关注热度甚高的先进金属新材料。长期以来,成分不断更新、工艺不断改进,但依然迈不过规模应用这道槛,特别是大面外观件,只有少量顶尖品牌的高尔夫球头才会采用。
由于涉及到零件平整度、水口切割,镀膜抗划伤等多个方面,业界没有成功经验可借鉴,开发过程异常艰难,人拉肩抗,产品良率低到供应商都准备放弃,关键时刻,团队坚持初心,顶住压力,充分拉通公司内部专家和业界TOP资源,导入镭雕整形,精密切割和硬质PVD镀膜等先进制造工艺。经过半年漫长而艰难的攻关,我们实现了非晶工艺能力质的提升,在业界第一次彻底打通大面非晶外观件全产业链。折叠手机转轴非晶门板件,也成为全球业界第一个真正规模量产的非晶大面外观件。
转轴非晶门板材料镀膜的超高耐磨要求是一个接踵而至的巨大挑战。为匹配整机颜色,非晶门板选用黑色偏蓝膜。而且,通过整机及转轴产品要求分解下来的外观材料性能需求,耐磨性能要达到传统膜层要求的10倍以上,要求整整高了一个数量级!
经过数月的业界广泛试产,仍然没有一家厂商可以满足转轴门板所要求的耐磨性能指标。我们只好从气相沉积膜层设备原理和膜层结构及成分进行分析,重新开发,广泛甄选业界顶尖PVD(物理气相沉积)厂商。最终采用了业界高密度等离子膜层沉积设备,设计了比瑞士军刀所采用的马氏体不锈钢更硬更耐磨的涂层结构,才初步满足了转轴门板件的耐磨要求。
到了转轴成品组装阶段,各种问题层出不穷,我们兵来将挡,水来土掩,从设计到制造全流程分析原因,改善设计和组装工艺,并跟踪问题闭环,在问题解决的过程中不断总结出如“渐进式预磨”、“精密尺寸整形补偿”等组装经验,组装过程关键检验工序从数十项增加至近百项,最终保障了产品的成功交付。
五、后记
直到今天,过去3年多来大家共同奋战的一幕幕,还仿佛就发生在眼前:在北京拉着厂商挑灯夜战,在上海争论技术问题互不相让,在深圳手动弯折样机几小时不停,在松研所画图赶工到半夜,在生产现场通宵跟线……
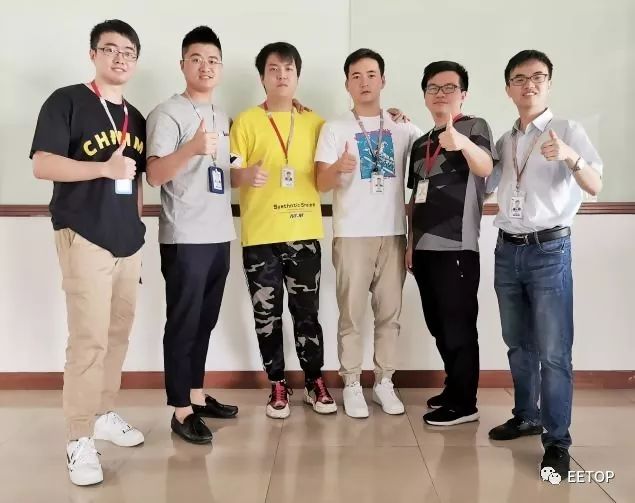
这一段全球独创、精雕细琢的鹰翼式转轴研发创新历程,满足了人们对未来美好生活的渴望,具有新的划时代意义!我们相信,无论前路有多远,山有多高,只要认准方向,尽最大的努力攻坚克难,就没有走不通的路,没有翻不过的山!而给消费者带来真实、有价值的创新,就是世界上最酷的事情!
【散热篇】给Mate X手机插上“飞鱼鳍”Mate X热设计团队
华为Mate X终于要进入公众视野了,作为参与其中的热设计团队,虽然我们只是其中的小小一环,却无比激动。
在两年多的时间里,面对巨大的散热考验,热设计团队里的每个人,都仿佛在冰与火中淬炼前行,一点点靠近最佳方案,最终通过“飞鱼鳍”的散热设计,解决了折叠屏手机高难度的散热难题。这一段不得不说的历程,回想起来,依然心潮澎湃。
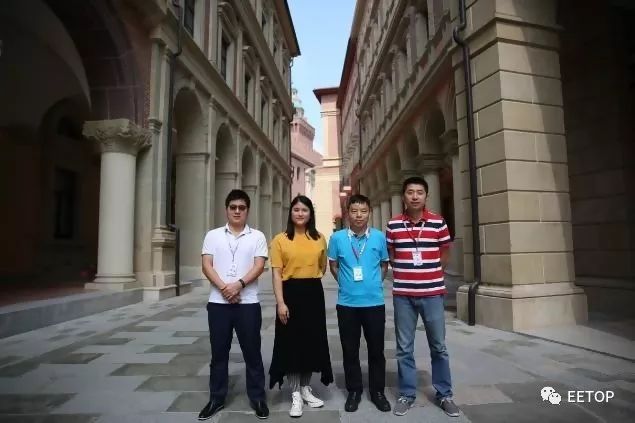
高颜值的“烫手”难题
为让折叠屏手机具有高颜值,华为ID设计团队颇费苦心,经过数轮迭代,最终确定采用非对称的关键元器件布局方案,让关键元器件集中布局在手机一侧,解决摄像头摆放问题,避免机身凹凸不平,带来全面屏、无刘海、超薄的极致用户体验。
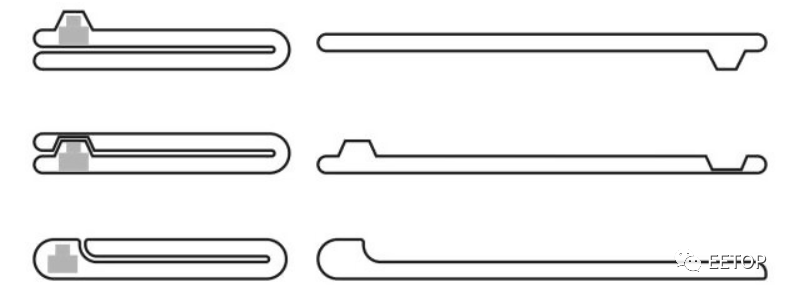
图1:几种方案的对比图
折叠手机初看,摊开之后面积会变得很大,手机外壳与空气的接触面积大会更加有利于散热,实际上却比常规直板机的散热更加困难,其原因有二:
一是折叠手机一旦折叠起来,厚度相当于翻倍,所以单层必须做薄到极致。可这样一来,内部的发热器件就离手机外壳更近。这就好比同一个太阳系中,靠近太阳的水星表面温度450℃+,而距离稍远的地球温度更适宜人类生存。在极致的超薄空间,理想的散热部件根本塞不进去,巧妇也难为无米之炊。
二是折叠机手机主板布局只能放在一边,这样会导致绝大部分发热器件都集中在一侧,热得“烫手”,而另外一侧基本不升温。第一次热仿真的结果印证了我们的预计:主板的一边,尤其是SOC(系统级芯片)区域的表面温度,已不是人体能忍受的范围了,另外一边却基本不会升温,温差之大简直就是“冰火两重天”。“太薄了,相当于手直接摸到器件了!”负责项目的工程师小吴感叹道。
“这个厚度下,散热很困难,器件到手机表面距离都不到1毫米了,我觉得应该建议项目组增加手机厚度,同时在手机外壳增加均温导热材料。”有同事提出了看法。
“我同意,同时应该建议把手机中框,做成导热性能更好的铜合金材质,代价是重量增加一部分。”另外一个同事附和道。
“我们做的是新形态的手机,不能完全用常规直板手机的思维,加厚、加重手机固然能解决散热,但是对颜值、用户感受是有很大牺牲的。”专家老李提醒道。
此话一出,大家压力倍增,但同时也明白,在不牺牲用户体验的基础上解决散热势在必行。目标确定,却是从未有过的挑战,热团队展开了多次的研讨。
要解决单侧大热源散热问题,大家首先想到的是“液冷”,即用金属液冷管将发热最猛的SOC热量,导到主板侧其他位置,再辅助外壳石墨贴附的均温方案,将主板侧外壳的温度做到均匀。这就好比摊煎饼,直接用火烤煎饼的一部分,很容易导致温度过高而烧糊;但如果把煎饼放在平底锅上,用火烤,煎饼各个位置受热均匀,熟得快也不容易烧糊。我们的液冷、石墨等方案就相当于将手机做成温度更均匀的平底锅,不轻易糊掉。
当然,对于折叠手机而言,为了不增加厚度,液冷管长度、厚度、拐角均要挑战设计极限。我们后来还为此特地设计了一根液冷管,长度约100毫米、厚度不到0.4毫米。
但是,这样就能搞定了吗?
“飞鱼鳍”创意的诞生
我们将方案建模仿真后,发现主板侧SOC处的局部温度确实下降不少,但是依然很热,并且仍然存在转轴两侧“一冷一热”温差窘境,因为没有方案能跨过转轴将热量传递。这就像是剃头的担子一头热,如何让扁担传热?
大家继续天马行空地发散思维。
“能不能找到一种导热良好且能承受多次弯折的材料,搭接在手机两侧?这样就能把主板的热量过渡一部分到另一边。”一向脑回路清奇的小吴率先发言。
“不行,导热金属承受不了不断弯折的考验,做薄会改善一些寿命,但是导热能力会下降很多,不靠谱!”有多年经验的兄弟对方案做出了评价。
“导热能力足够的金属显然行不通,把折叠机绑定在一个铜板上,还能折得动么?太影响手感了!”
“非金属也不行啊,也耐不住多次弯折的。”
……
大家你一言,我一语,几乎可以认定,没有一种材料能满足兼顾导热,可弯折且长度自由变化。对业内相关的折叠散热解决方案进行全面调研后,更是确认了这一点。
“我们能不能对导热材料进行一些特殊的设计,让它具备折叠的特性呢?比如钢筋不能弯折,但是我们做成铁链后就能折成任意形状?”专家老李不肯放弃,鼓励大家:“既然没有路,随便开拓一片荒原就是路,走错了没关系,大家一起开垦,总有正确的方向!”
用常见金属实现跨轴导热,必然影响折叠手感体验,增加重量且可靠性差;
用常见非金属如石墨导热,不能实现长度自由收缩,且可靠性差;
能实现自由弯曲伸缩,基本只有橡胶一类的材质,然而不具备导热能力;
但如果按照老李说的,把导热材料的弯折区域进行结构化设计加工,说不定会具备耐弯折且自由伸缩的特性。
于是大家按照自己的理解,提出了多个设计的idea。有的类似折扇,有的像双节棍,有的像弹簧。
“我觉得鱼鳍的结构更具有代表性,”充满想象力的小吴在讨论中说出了她的想法,同时走到白板处向大家画图示意:“把导热材料中间区域,做成收缩形状的鱼鳍纹路,手机折叠时能收拢,手机展开时又能不太费力地拉伸开来,这样既不会影响手机开合手感,导热性能也不会下降。”
我们至今仍然深深记得会议室小白板上各种方案的对比分析,大家在上面不停涂涂抹抹,擦掉又重来。经过长达两周的论证分析与仿真,我们一致认为,把传统导热材料进行类似于“鱼鳍”的仿生结构化加工,是有可能实现耐弯折、回弹良好的目标的。
样品必须神形兼备
然而,这种仿生结构如何加工出来?这是方案面临的最大难题。
为了论证清楚方案可行性,接下来的几个月时间,我们不断与行业专家交流方案,从材料选取、仿生结构设计、如何生产加工、如何组装等多方面做了研讨。同时,为了尽快做出方案demo,我们展开了与供应商的技术合作。当技术需求传达给供应商工程师的时候,对方表示,从来没有接触过这种需要结构化设计的导热材料。
大家一起确定了需要解决的两个关键问题:一是这种仿生结构如何加工;二是材料长期在不断的弯折回弹过程中必然存在变形,如何确保长期使用后依然回弹良好,这就好比一个弹簧,长期拉扯变形,收缩能力必然会打折扣。
要将这种仿生结构加工出来实现量产,只能匹配设计相应的模具来加工,采取“鸟枪法”,即不断设计尝试多种模具参数加工,看哪种方案加工出来的结构最符合形态特征。起码要达到外观“长得像”,并且加工后材料性能不受影响。经过一系列的尝试,我们选出了其中最靠谱的一种。但是轻轻拉扯了几下,“鱼鳍”就完全变形,根本没有回弹性能,更别说放在手机里承受数万次拉扯与弯曲!
我们都很失望。仅仅形状“长得像”是徒有其表的,要让它真的实现回弹收缩才是神形兼备,这也就是我们前期预想的第二个关键问题。
这个棘手的问题让大家一筹莫展。我们只能用笨办法,常驻供应商处,不断尝试各种可能的材质。终于,一个多月后,我们接到驻厂同事小刘的电话,语气中透着兴奋:“找到合适的材质了!复合后回弹效果不错,已经测了一万次了,没有问题!”
紧接着,我们拿到批量样品,一系列的耐弯折测试展开。在10万次反复弯折的情况下,样品没有任何磨损变形,导热性能依然良好,这让我们总算心里有了底气。自此,新形态折叠手机的热解决方案翻开新的一页。
量产挑战业界极限加工能力
2018年方案转为量产,面临的问题也更加突出,技术方案究竟能否实现量产,转化为商业应用呢?这个问题一直拷问着大家。
还没开始试制,问题就来了:由于这种有特殊结构的材料,不同于其他导热模切材料,制作过程异常复杂。普通材料要实现量产生产,1到3把刀具就可以,但我们的材料要实现量产,至少需要20多把刀具,超出当前业界的极限加工能力。这就好比是绘画,之前我们让供应商画的都是水墨黑白画,不管什么图案,一种颜料就能搞定,现在要画五彩斑斓的油画,颜料繁多,顺序复杂,复杂度成为了加工极限。
方案太复杂了,需要简化!
“罗马不是一天建成的,却是一块块砖垒起来的,只要搞清楚每块砖堆的顺序,我们就有办法去优化”,参与项目的小刘很快奔赴供应商,检查“每块砖”是如何堆成的。
在试制过程中,我们不断与供应商、工艺同事交流优化方案,在保证性能、可组装的基础上优化制程,争取每一道制程的刀具功能最大化,把每道制程抠出来看能否优化。经过14次的修模优化,长达7个月的方案迭代,终于让制程稳定,让方案可量产化。
给手机插上“飞鱼鳍”
技术已实现量产,但要把这种“鱼鳍”装进手机,还需要解决装配上的难题:“到底是在手机折叠的时候装配,还是在展开的时候装配?展开状态下装配普通夹具,造成拉伸变形的问题怎么解决?折叠状态下装配,怎么能准确定位?怎样装配对转轴不会有影响?”一个接一个的问题。专家老施出谋划策,和工艺同事充分验证,不断攻关尝试,设计了能准确将“鱼鳍”装进手机的专用夹具方案。甚至,针对材料运输过程中可能出现的问题,经验丰富的“老司机”旺哥还对包装做了针对性设计。
在一次又一次的优化攻关中,我们终于将小吴想象中的“飞鱼鳍”装进了折叠手机。实测效果与预期吻合,既可实现弯折,又能将手机主板侧的热量,跨过转轴导到另一边,手机降温效果明显。
这是一次大自然智慧与华为工程师的完美互动,也是热设计团队对于用户体验的执着追求。
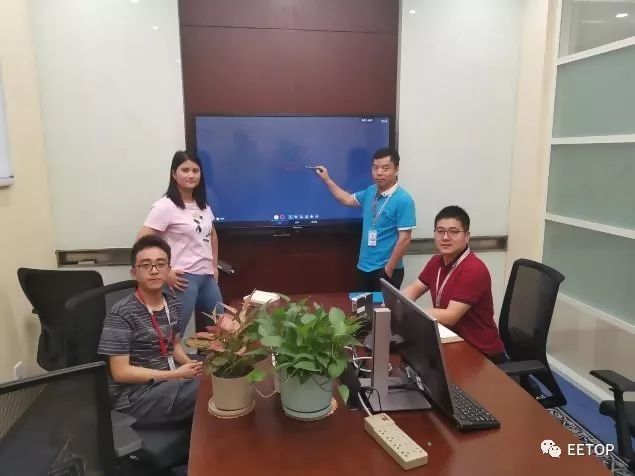
回首整个过程,无不充满着奇幻的想象与百折不挠的尝试。放眼未来,更多的挑战等待着我们。要做出引领业界的极致产品,我们将踏足更广袤的荒原,我们将把更多的想象力装进产品,给用户带来极致的体验!
*免责声明:手机市场分享转载仅为了传达一种不同的观点,不代表手机市场分享对该观点赞同或支持,如果有任何异议,欢迎联系手机市场分享。